Пресс-день инноваций
30 апреля 2013, Оксана Демченко
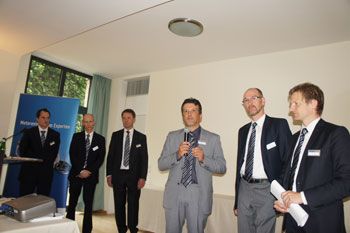
Корпорация Federal Mogul выбрала свой особенный подход к презентации инновационных идей и технологий, собрав в Нюрнберге группу журналистов со всей Европы и присоединив к ним представителей стран СНГ. Для прессы, работающей именно в интересах профессионалов автоотрасли, подготовили доклады ведущие специалисты концерна, инженеры и технологи, разработчики самых современных продуктов различных брендов и направлений из широчайшего спектра компетенций Federal Mogul. Но, как принято говорить в рекламе, и это еще не все: журналисты посетили завод по производству поршней.
Основная тема, вокруг которой структурировалась программа мероприятия, была заявлена как «Новейшие технологии для экологичных двигателей», что подразумевало ориентированность всех разработок корпорации на сокращение ущерба для окружающей среды как на этапе подбора материалов и формирования производственных стандартов, так и в последующей эксплуатации автомобиля с инновационными системами и деталями. При концентрации внимания на сокращении выбросов «главными понятиями» дней инноваций стали эффективность (снижение всех видов потерь) и downsizing (компактность), то есть в целом – изменение подходов к проектированию двигателя. Опираясь на указанные тенденции, инженеры последовательно предлагали вниманию журналистов взгляды на различные системы и детали именно с точки зрения новых подходов, задающих направление конструкторской мысли.
Поршни, технологии на сегодня и на перспективу
«Даунсайзинг двигателя – это не просто изменение размера деталей и рост компактности силового агрегата. Это совершенно новые условия работы для цилиндро-поршневой группы, гораздо более жесткие, требующие новых материалов и технологий», – так сказал Арнд Баберг, руководитель направления по развитию технологий и дизайна поршней. Сразу отметим: под дизайном имеется в виду не упаковка или «красивый внешний вид», а та специфическая форма, которая позволяет поршню выдерживать растущие нагрузки. В сокращении выбросов СО2 среди всех продуктовых групп концерна именно поршни и кольца позволяют достичь наибольших прямых результатов: суммарного сокращения выброса на 4,4 грамма с километра пробега по бензиновым двигателям и 2,5 г/км для дизелей. Много это или мало? Давайте разберемся, заодно учитывая и иные условия.
Выделив как конечный запрос клиентов-авто-производителей снижение выброса СО2, господин Баберг подразделил задачи по достижению этой цели на входящие в компетенцию концерна и находящиеся для него во «внешней» среде. Так, производитель поршней не может требовать от партнера применения в системе охлаждения помп с электрическим приводом, сам не участвует в их разработке и модернизации. Зона его прямой компетенции понятна, и его главная задача в рамках этой зоны – сокращение потерь на трение. Решать эту задачу надо в условиях продолжающегося даунсайзинга, делающего двигатель все легче, компактнее. С точки зрения технологий перечисленное означает следующее:
- рост удельной мощности (в перспективе до 100 кВт с литра объема);
- рост давления впрыска (в обозримой перспективе до 220 бар);
- рост термических нагрузок;
- работа деталей в крайне неблагоприятном режиме старт-стоп и учет иных потребностей гибридных силовых установок;
- необходимость учета ситуации с увеличением сервисных интервалов;
- жесткие условия по лимитированности цены конечного продукта (детали, системы в целом);
- рост температуры отработавших газов и специфические технологии работы с ними (дожиг, например);
- проектирование деталей и узлов под современный глобальный рынок, где на уровне автопроизводителей и их альянсов идет все более обширная унификация и выработка единых «платформ».
Для практиков авторемонта перечисленное еще раз дает повод задуматься о надежности партнера по поставке запасных частей, поскольку усложнение двигателя уже не допускает компромиссов по качеству. И ничуть не случайно то, что дни инноваций прошли в городе, где завод Federal Mogul в минувшем году произвел более 11 млн поршней, поставляемых на конвейеры ведущих автопроизводителей и известных специалистам вторичного рынка под брендом Nural (что собственно и есть сочетание первых букв названия города Нюрнберг и обозначения алюминия).
Для инженеров-разработчиков цилиндро-поршневой группы перечисленные чуть выше общие условия трансформируются в более конкретные, как технологические, так и управленческие: рост механических нагрузок на поршень и ужесточение термического режима (до 420°С в наиболее нагруженной зоне); потребность следовать за глобальным автопроизводителем в плане снабжения сборочных заводов, обеспечивая одинаково высокое и стабильное качество на всех своих предприятиях, независимо от рынка и страны; необходимость создавать очень точные логистические системы с минимумом издержек и потерь.
Наконец, переходя к уровню собственно инженерных решений, следует говорить уже о поверхностном упрочнении и работе со структурой; создании алюминиевых сплавов, стойких к механическим и термическим нагрузкам; росте требований по износостойкости, в том числе в критических режимах; применении технологий локального, зонального усиления; борьбе с кавитационными эффектами и оптимизации формы для дальнейшего снижения веса без потерь прочности.
Применительно к поршням дизелей топовым решением можно назвать технологию Monosteel, такие поршни уже используются в сверхмощных дизелях массово (произведено более 3,5 млн поршней). Продолжением развития технологии станет новое ее поколение – Magnum Monosteel. Для производства поршней из алюминиевого сплава применяется фирменная технология «горизонтального литья», позволяющая получить высокую однородность изделия, избежать образования дефектов и увеличить точность позиционирования вставок-усилителей в зоне первого поршневого кольца, безошибочное размещение солевых колец, создающих в дальнейшем галереи охлаждения. Заслуживает внимания сама идея и технология «галерей охлаждения» – круговых каналов, пролегающих близ наиболее горячих участков поршня и позволяющих доставлять туда масло и эффективно снижать температуру, одновременно облегчая поршень. Галереи формируются на месте вложенных в форму для литья упомянутых выше солевых колец (температура плавления этого материала много выше той, при которой подается жидкий алюминиевый сплав). В дальнейшем солевое кольцо просто вымывается: ведь соль растворима в воде.
Для исключения дефектов готовой продукции на заводах используется неразрушающий контроль поверхности, дополненный ультразвуковым двухмерным контролем (награда РАСЕ 2012 за эту технологию), сверяющим с эталоном геометрию, положение галерей, бездефектность литья. Высоконагруженные поршни проходят дополнительное упрочнение части «короны» при помощи технологии DuraBowl: лазерного прогрева уже сформированных поверхностей до точки плавления, позволяющего существенно улучшить структуру материала и повысить его прочность. В частности, при прогреве в десятки раз уменьшается размер частиц кремния в зоне воздействия, что повышает и долговечность поршня.
Как перспективные, находящиеся в проработке господин Баберг отметил технологии поршней со сверхнизкими параметрами трения. В отношении поршня бензинового двигателя господин Баберг подчеркнул высокую роль инженерного дизайна, оптимизирующего в первую очередь форму зоны юбки и ее покрытий.
Кольца: все тонкости технологии
«При сохранении актуальности базовых задач поршневых колец по уплотнению и контролю расхода масла, – отметил господин Йоханнес Эссер, руководитель направления поршневых колец и гильз, – инженерам приходится решать проблемы исключения прорыва газов, минимизации износа даже не в паре, а тройке трения кольцо – поршень – стенка цилиндра». И все это при условии роста компактности конструкции, нагрузок. Для решения специфических задач в каждом сегменте двигателей по цене и нагруженности используются различные материалы кольца, технологии производства, дизайны и покрытия. На рынке сосуществуют в своих нишах кольца из чугуна, высокопрочных сталей. Оптимизации их свойств способствуют технологии упрочнения, покрытий и собственно геометрии колец.
«Специалист сервиса, пусть и весьма грамотный, невооруженным глазом не способен оценить наши усилия, – посетовал господин Эссер. - В сечении кольцо представляется ему прямоугольником, а цвет и любые иные подобные характеристики более чем условны. Подлинное качество – это не то, что мы ощущаем. Это доверие к бренду, к дистрибьютору и самому каналу поставки. Поршневые кольца – продукт высоких технологий, и это важно помнить. Вот лишь несколько фактов для оценки сказанного. В 1985 году толщина «типового», взятого за пример верхнего кольца бензинового мотора составляла 1,75–3,55 мм. Кольцо выполнялось из чугуна (часто высокопрочного) и имело хромированное покрытие. Маслосъемное кольцо из чугуна было толщиной 2,0–3,55 мм. Набор мог дополняться и третьим кольцом толщиной порядка 3 мм. В 2010 году колец остается два, верхнее выполняется из азотированной стали, имеет сложное покрытие в технологии DLC и толщину 1,2–2,9 мм. Маслосъемное кольцо чугунное, тоже с покрытием DLC и толщиной 1,5–3,0 мм. Такое изменение «комплектации» способно обеспечить снижение локальных потерь на трение до 70%!»
Буквально несколько слов о покрытиях, ведь их, в отличие от дизайна, нельзя наглядно продемонстрировать на рисунках. Из ноу-хау стоит отметить созданные инженерами Goetze покрытия CKS (хромокерамическое) и новое поколение покрытий на основе CKS – GDC («алмазное покрытие»), обеспечивающее высочайшую износостойкость, по оценкам концерна, четырехкратно превышающую стандартные хромированные покрытия и вдвое – хромокерамические.
А вот примером торжества инженерного дизайна стоит назвать маслосъемное кольцо LKZ-Ring, получившее в 2011 году награду PACE. Исходно оно создавалось под жесткие условия работы современного высоконагруженного дизеля, но стало успешно применяться и для бензиновых моторов с прямым впрыском.
Подшипники и старт-стоп
Это пример того, как взаимодействуют различные технологии при минимизации выброса СО2. Система «старт-стоп» распространяется на рынке, переходя из премиального сегмента в бюджетный. Она позволяет существенно сократить любые вредные выбросы в наиболее критичных условиях пробок, городского движения со светофорами. Однако «побочным эффектом» указанного достижения оказываются не просто жесткие, но экстремальные условия работы ряда деталей двигателя. И в первую очередь вкладышей. Именно вкладыши – одна из основных продуктовых групп бренда Glyco, входящего в портфель Federal Mogul. Оказывая лишь косвенное влияние на снижение выбросов, сами вкладыши нуждаются в инновационных технологиях, чтобы эту глобальную тенденцию поддержать. Ведь каждый пуск – это масляное голодание, даже вероятность работы «всухую». И так – несколько десятков или даже сотен раз в день, по сути, на каждом светофоре и даже пешеходном переходе! Износ вкладышей несоизмерим с тем, который характерен без применения «старт-стопа». Так что же, отказаться от системы? Или, как предложили инженеры Glyco, создать подложку из полимерного покрытия IROX, способного короткое время без ущерба работать без масляной пленки, выдерживающего высокие нагрузки и температуры. Испытания в режимах, в том числе подобных «старт-стопу», показали пятикратный рост ресурса в сравнении со стандартным вкладышем.
Ну и небольшая ложка дегтя в эту бочку меда: пока технология доступна лишь для первичного рынка, срок начала поставки на вторичный, надеемся, придет очень скоро.
Вообще многие решения начинают развитие именно на конвейере. Например, ставший нормой для Европы с 2011 года запрет на использование содержащих свинец материалов, коснувшийся производства вкладышей. Современные вкладыши от Glyco производятся из бронзы, не содержащей свинца. Это важно с точки зрения охраны здоровья, но одновременно это позволяет получить и прирост полезных свойств материала: устранена пористость структуры, максимальная несущая способность, по оценкам инженеров концерна, выросла на 20%.
Большой мир авторынка и его часть – ремонт
Для конечного клиента очень часто технологии, создающие новизну и инновационность его автомобиля, остаются невидимками. Для профессионала ремонта они должны быть понятны и как часть развития отрасли, и как фактор, помогающий исполнять работу без риска рекламаций. Все более сложные системы позволяют расходовать меньше топлива, выбрасывать меньше вредных веществ, реже посещать СТО для техобслуживания. Но эти же технологии задают очень высокую планку по качеству запасных частей, квалификации мастеров, подбора технических жидкостей и так далее. Работа механика становится подобна труду не хирурга, готового «отрезать и пришить» без колебаний, а врача общей практики, сильного в диагностике и подборе терапевтических средств. А это, повторимся, – надежные связи с партнерами, доступ к технической информации «из первых рук» и просто доверие к продукции…
Еще никто не оставил свои комментарии. Ваш комментарий будет первым.